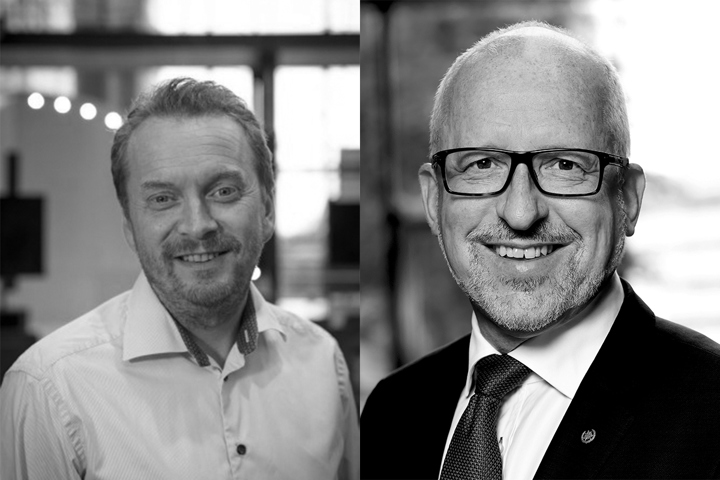
Covid-19 – an “unknown-unknown” that challenges global supply chains
18 January 2021
A sustainable and continuous supply of products, materials, and services is at the heart of supply chain design in the manufacturing and service sectors. The Covid-19 pandemic has brought disruption on a scale that is hard to grasp. Erratic national lock-downs, shut-downs of factories, customer order cancellations, and frequently interrupted flows of materials and goods are widespread. Physical interactions with the customer-base have gradually diminished. Not only have operations of global supply chains come to a halt, but operative principles and boundaries of well-established practices are also being re-defined.
The inter-connected nature of current supply chains has been shaped by globalization, supply chain optimization, Lean thinking, sustainable development, digitalization, and servitization. Fluctuations and disruptions have to a large extent been “manageble-knowns” or “knownunknowns”, ranging from seasonal variations and supplier quality problems to severe issues such as product recalls and environmental incidents. Paradoxically, what used to be a strength in an era of growth and stability, has become a vulnerability in the Covid-19 crisis. Social distancing of people is being enforced to reduce risks of further spread of the disease with impacts that propagate directly and immediately to higher levels; in processes, in organisations, and across supply chains.
An “unknown-unknown”?
Covid-19 and its impact resembles an “unknown-unknown” or a so-called Black Swan event. Contrary to the financial crisis of 2008, this disruption has been immediate rather than emerging and the health of individuals (and not only businesses) is at risk. Both supplier networks and customer markets are affected, predictability is low, and the longevity of the virus is uncertain. Moreover, economic history has not provided us with useful strategies based on previous experience and there was little time to investigate early warning signs. These are just a few of many circumstantial dimensions of the crisis.
Transilience – a new take on responsiveness
Early into the pandemic we talked about “response”, “mitigation”, “a new normal”, the “big restore”, and “resilience”. Currently, at the verge of a new wave of the pandemic, we may need to revise our approach. Based on our review of current state of theory and practice, a key ability to meet further challenges and exploit opportunities can be summarized in terms of “transilience”. Design of supply chains should ensure that they are managed rapidly, restoring some processes while simultaneously radically changing others. We have identified four potential pathways to promote restoration and change:
(1) Regional supply chains: The shutdown of borders and delays in transport have revealed how Covid-19 reinforces geopolitical risk, despite trade agreements and countertrade. One response is to make supply chains more regional, serving particular markets, allowing for decentralized and rapid decision-making. This provides an immense opportunity to reset and re-think sustainability of transportation and to adapt processes to work with social distancing.
(2) Project-based supply chains: During an emergency, supply chains must be capable of reverting from continuous flow into projectbased settings. Short-term layoffs mitigate impact on costs and revenue-generating activities. But a truly agile and temporary arrangement is needed to aid managers in de-coupling of disruptive impact, reverting “shut-down” into “slow-down”. This includes volume decrease in production to avoid tied-up capital as well as remote working and a slowing down of responses to customer’s service requirements. Companies can also share capacity and personnel to maintain the required levels of operation. Finally, establishing closer collaboration with customers is needed to manage panic-ordering and to attend high-priority customer segments.
(3) Radical shift supply chains: Six months into the pandemic, supply chain designs fostering “new windows of opportunity” seem to center around processes, services and a strong customer focus. Social distance through increased automation in production is one example. Other shifts refer to business models, digital technologies, and visualization. One example is the use of digital technology to enhance remote service delivery in aftermarkets. Another example is re-skilling of R&D personnel to speed up the shift in skills that is needed to produce electric vehicles, enhancing rapid electrification of the transport sector. (4) Critical supply chains: The ongoing Covid-19 crisis has demonstrated great industrial ability and willingness to take on social responsibility for the wider society. Industrial supply chains are adapted to respond to immediate demands of global crisis. One example is ensuring operational food supply chains able to respond to the panic-buying in retailing. Another example is the repurposing of production and distribution of e.g. perfume and cars into the provision of critical supplies such as hand sanitiser, ventilators, face masks, and medicine. This way, industrial supply chains become core enablers of national and governmental readiness for humanitarian aid, providing both capacity, resources and materials to beneficiaries.
Never waste a good crisis
Historically, “unknow-unknowns” have resulted in social crises, reorientation, and societal disasters. However, each reorientation contains huge potential for paradigm shifts and new business models on societal, industrial, and individual levels. We have provided four ways to reevaluate and reposition supply chain thinking. Let us continue to use the Covid-19 crisis to create a more sustainable and resilient society.
CHALMERS UNIVERSITY OF TECHNOLOGY
SCC member Chalmers University of Technology in Gothenburg conducts research and education in technology and natural sciences at a high international level. The university has 3100 employees and 10,000 students, and offers education in engineering, science, shipping and architecture. Learn more at www.chalmers.se.
BY: Árni Halldórsson, Supply Chain Management Professor and Johan Stahre, Chair of Production Systems, Chalmers University of Technology, Sweden.
Join our mailing list
and keep up-to-date with the Chamber's news and events.
Read our Privacy Policy here